Motoreninstandsetzer kümmern sich nicht nur um komplette Motoren. Zum Tagesgeschäft gehören auch angelieferte Einzelteile wie Zylinderblöcke, Kurbelwellen, Pleuelstangen oder auch Zylinderköpfe. Hierbei ist nicht immer ein Motorschaden Voraussetzung, auch regelmäßige Wartungen an bestimmten Motortypen können Anlass für die Demontage eines Kopfes sein. Hier ziehen viele Werkstätten die Spezialisten der Motoreninstandsetzung und ihren Maschinenpark heran.
Angeliefert wird ein John Deere Zylinderkopf. Die auf 6 Zylinder verteilten 24 Ventile bitten um Augenmerk und etwas Pflege, welcher sich das Team der Motoren Henze GmbH in Hannover gerne annimmt.
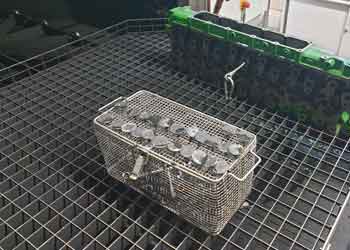
Der vom Kunden soeben angelieferte Zylinderkopf wird – wegen seines hohen Eigengewichts von ca. 120 Kg – mit Hilfe eines Transportwagens zur ersten Sichtprüfung in die Werkstatt gebracht. Hier richtet sich das Augenmerk auf den Gesamtzustand, eventuelle grobe Beschädigungen und den Zustand der einzelnen Gewinde. Ein Erstbefund wird erstellt und der weitere Bearbeitungsweg festgelegt. Von hier aus geht es für den John Deere Kopf erst einmal in die Wäsche. Ölrückstände, Fette und weitere Verschmutzungen an Flächen, im Kühlkreislauf etc. werden entfernt.
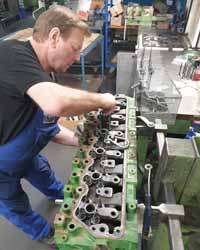
Nach der gründlichen Reinigung geht der Weg in die Demontage. Die Ventilfedern werden nun vorsichtig mit Spezialwerkzeug zusammengedrückt, um die einzelnen Ventilkeile entnehmen zu können und so Federn und Ventile vom Kopf zu trennen. Die Ventile werden begutachtet und die Entscheidung über die Bearbeitung oder die Beschaffung neuer Ersatzteile getroffen. Letzteres ist in diesem Fall aber nicht nötig.
Nun wird der Zylinderkopf selbst geprüft. Werkstätten sprechen hier allgemein von „abdrücken“ oder auch „wasserprüfen“.
Was dahinter steckt: Der Kühlkreislauf wird mit Dichtplatten verschlossen, an einer Stelle wird zusätzlich ein Druckluftanschluss montiert. Der Zylinderkopf wird in das Wasserbad herabgesenkt, welches auf ca. 70°C aufgeheizt ist, um den Kopf gleichmäßig zu erhitzen und damit eine gewisse Arbeitstemperatur zu simulieren. Nachdem der Zylinderkopf eine Weile temperieren konnte, werden nun bis zu 5 Bar Druck auf den Kühlkreislauf gegeben. Jetzt entscheidet es sich.
Befund: Keine Bläschenbildung, keine aufsteigende Luft im ruhigen Wasserbecken, also keine Risse im System. Der Kopf hat bestanden und kann weiter überarbeitet werden.
Notiz am Rande:
Diese Prüfung gibt keinen Status über den Zustand der Zylinderkopffläche selbst, oder ob der Zylinderkopf eventuell „verzogen“, also in sich verformt ist. Die Rissprüfung stellt lediglich sicher, dass der Kühlkreislauf keine Leckage zum Rest des Systems aufweist!
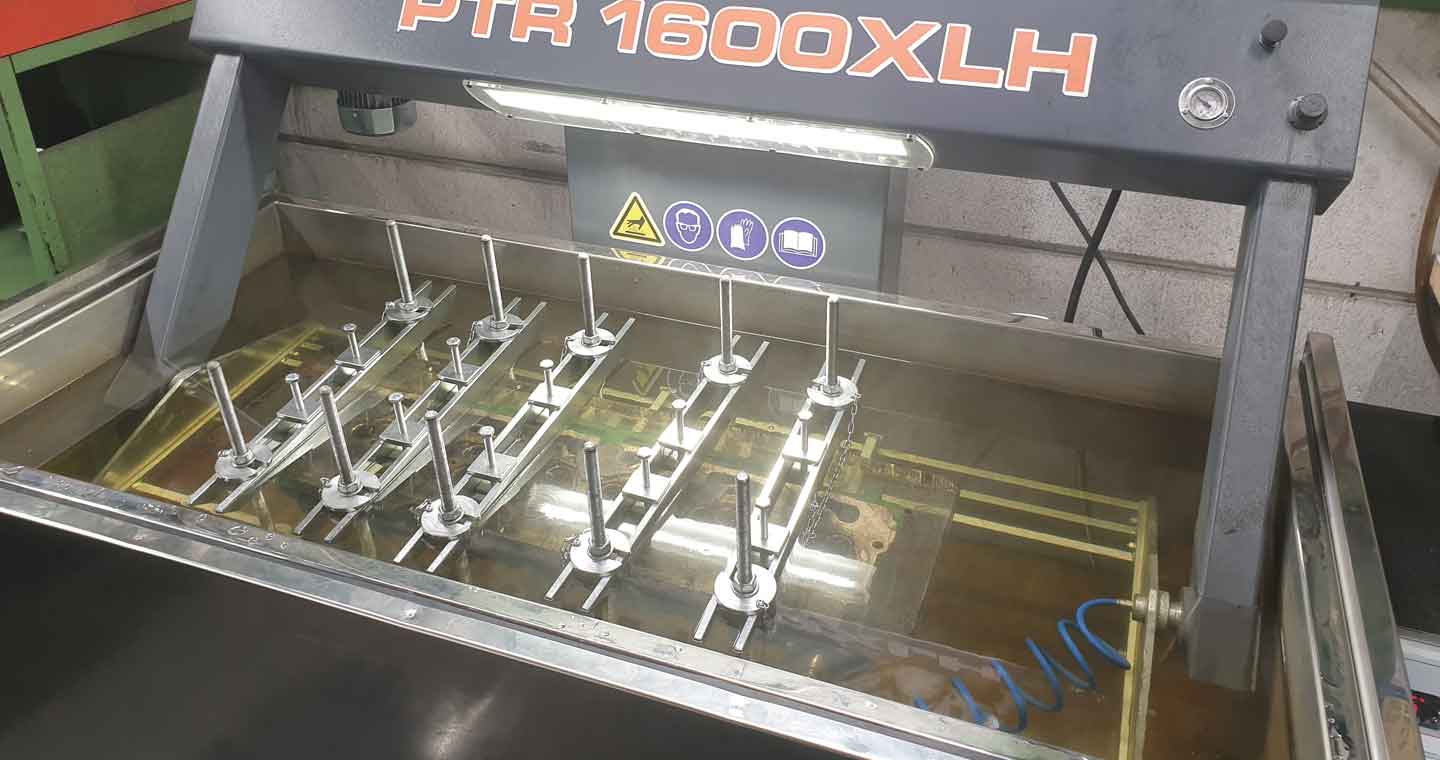
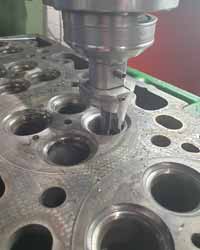
Nächster Arbeitsschritt: Ventilsitze prüfen und nachfräsen, ggf. Ventilsitze erneuern. Die einzelnen Ventilsitze werden auf vom Hersteller angegebene Sitzwinkel gefräst, welche sich später genau mit den entsprechend gegenliegend geschliffenen Ventilen ergänzen und so absolut dicht aneinander liegen werden. Hierbei kommt es auf Genauigkeit an. Die Maschinen müssen – und das können sie natürlich auch – extrem genau und verlässlich arbeiten und von gut geschulten Fachleuten bedient werden.
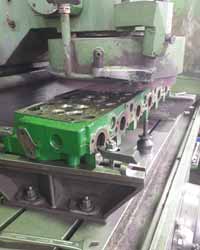
In diesem Bearbeitungsschritt werden auch die Ventilführungen überprüft und gegebenenfalls gewechselt. Außerdem werden die einzelnen Gewinde am Zylinderkopf geprüft und falls notwendig direkt instandgesetzt. Das Team hat dank spezieller Werkzeuge und dafür expliziter Ausbildung die Möglichkeit, Gewinde an Köpfen, Gehäusen etc. nicht nur nachzuarbeiten, sondern auch z.B. abgerissene Stehbolzen mit Hilfe der Senkerodierung zu entfernen. Alternativ können defekte Gewinde unter Einsatz von Time-Sert-Buchsen (diese sind deutlich stabiler als die weiterverbreiteten und bekannten Heli-Coil Gewindeeinsätze!) wieder auf das passende Maß instandgesetzt werden.
Verfahren: Erodieren
Mit dem Erodiergerät lassen sich an Zylinderköpfen, Motorblöcken etc. abgerissene Metallteile mittels Senkerodierung entfernen. Dafür wird eine Kupferelektrode in den Schwingkopf eingespannt. Diese hat einen kleineren Durchmesser als das abgebrochene Werkstück. Beim Erodieren wird nur das Kernstück des Werkstücks abgebaut. Es besteht kein mechanischer Kontakt zwischen Elektrode und Werkstück, dadurch bleibt das Gewinde unbeschädigt und die Werkstückreste können entfernt werden.
Die Sitze sind überarbeitet, alle Gewinde wieder optimal, es kann geplant werden.
Der Zylinderkopf wird auf die Planschleifmaschine gespannt und ausgerichtet. Nun fährt in feinen Abstufungen der Schleifkopf mit den passend zum zu bearbeitenden Teil eingesetzten Schleifsteinen über die Kopffläche. Material wird im Hundertstel-Millimeter-Bereich abgetragen, bis eine einwandfreie und den Herstellervorgaben entsprechende Dichtfläche entsteht.
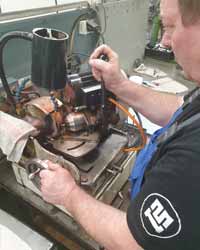
Parallel zur Kopfbearbeitung werden auch die Ventile überholt. Es wird kurz überprüft, ob diese auch wirklich in Ordnung sind und nicht eventuell einen Schlag im Schaft oder am Tellerbereich aufweisen. Dann werden die Schaftenden der Ventile sowie die Tellerränder nachgeschliffen. Die Ventilteller müssen bei der Montage genau zu den geschliffenen Ventilsitzen passen, um wirklich dicht abzuschließen. Präzisionsarbeit. Ob dies auch genau genug passiert ist, zeigt eine mit Unterdruck durchgeführte Prüfung. Am jeweiligen Ein- oder Auslasskanal wird eine Unterdruckpumpe angesetzt, welche einen vorgegebenen Wert erreichen muss, um die Prüfung als „erfolgreich“ abhaken zu können.
Notiz am Rande:
Früher wurde hierzu auch hin und wieder ein Flüssigkeitsverfahren angewandt, in welchem der Brennraum im Kopf mit den eingesetzten Ventilen gefüllt wurde. Die Flüssigkeit durfte nicht absickern. Dieses Verfahren ist jedoch vergleichsweise ungenau und wird heute nur noch im Privat- bzw. Hobbybereich angewendet.
Alle Arbeitsschritte und Prüfungen sind erledigt, der Zylinderkopf kann nun mit all seinen Einzelteilen einmal komplett gereinigt und zur Montage vorbereitet werden. Die Nachreinigung ist extrem wichtig, da durch die verschiedenen Fräs- und Schleifvorgänge Rückstände an Flächen und in den Kanälen vorhanden sein können. Anschließend werden alle Teile in den sauber vorbereiteten Montagebereich verbracht, wo der Kopf nun wieder komplettiert wird.
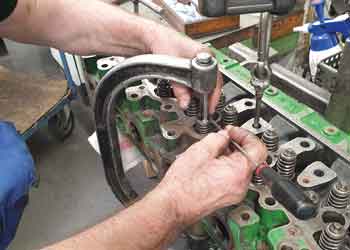
Die Ventilschaftabdichtungen werden auf die Führungen montiert, die Ventile passend eingesetzt und die Ventilfedern (der Druck einer solchen Feder ist so hoch, dass man diese nicht einfach mit den Fingern herunter drücken könnte!) mit Spezialwerkzeug und den Ventilkeilen wieder komplett montiert.
Der Zylinderkopf ist nun abholbereit und kann von der Werkstatt wieder auf dem Motor aufgebaut werden.//